Работа пружинных аппаратов основана на возникновении сил сопротивления упругой деформации пружин при их сжатии. Такие аппараты применяются только в упругих площадках пассажирских вагонов.
Работа пружинно-фрикционных аппаратов основана на превращении кинетической энергии соударяемых вагонов в работу сил трения фрикционных элементов и потенциальную энергию деформации пружин.
В аппаратах с резиновыми элементами эта энергия затрачивается на работу сил внутреннего трения резины.
В гидравлических (гидрогазовых) аппаратах кинетическая энергия удара затрачивается на преодоление сил вязкого сопротивления жидкости при перетекании ее из одной камеры в другую через калиброванные отверстия.
Выбор типа поглощающего аппарата для вагона определяется его параметрами: энергоемкостью, ходом, величинами начального и конечного сжатия, величиной необратимо поглощенной энергии, стабильностью и готовностью аппарата к работе (показатель заклинивания). Параметры поглощаю-щих аппаратов выбирают в соответствии с Нормами.
Энергоемкость аппарата представляет собой величину кинетической энергии, которую он воспринимает при полном сжатии.
После сжатия аппарата его подвижные части необходимо возвратить в исходное положение, поэтому они проектируются так, чтобы не вся энергия поглощалась необратимо. Это свойство оценивается коэффициентом необратимо поглощенной энергии. Коэффициент готовности аппарата определяется при испытаниях как отношение числа нагружений, при которых произошло заклинивание аппарата, к общему числу.
Показатель стабильности работы аппарата характеризует способность сохранять основные его параметры при многократных его нагружениях.
На вагонах железных дорог наибольшее распространение получили пружинно-фрикционные аппараты и аппараты с резинометаллическими элементами.
Пружинно-фрикционные аппараты широко применяются на грузовых и пассажирских вагонах, так как они просты по конструкции и надежны в эксплуатации.
Однако они имеют низкую стабильность работы и ограниченную энергоемкость при существующих габаритных размерах. Поглощающие аппараты с резинометаллическими элементами устанавливаются на пассажирские вагоны, так как они обеспечивают хорошую плавность хода при соударениях, высокую надежность и бесшумность работы.
Пружинно-фрикционные аппараты изготовляют по ГОСТ 22253—76. Для четырехосных грузовых вагонов выпускались пружинно-фрикционные аппараты типа Ш-1-Т (шестигранный, первый вариант, термообработанный) с энергоемкостью 3 = 26 кДж.
Затем начали изготавливать модернизированные аппараты Ш-1-ТМ (3 = 38 кДж). С 1979 г. на грузовые четырехосные вагоны устанавливают аппараты Ш-2-В (3 = 50 кДж, второй вариант, взаимозаменяемый). Восьмиосные грузовые вагоны оборудуют пружинно-фрикционными аппаратами Ш-2-Т (3 = 55 кДж).
Для восьмиосных вагонов разрабатывается новая конструкция пружинно-фрикционного аппарата энергоемкостью 200 кДж. Все типы пружинно-фрикционных аппаратов по конструкции аналогичны и отличаются в основном параметрами.
Аппараты Ш-1-ТМ, Ш-2-В и Ш-2-Т устанавливают в автосцепное устройство, имеющее стандартное расстояние между передними и задними упорами (625 мм).
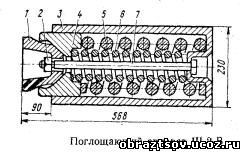
Аппарат Ш-2-В имеет литой корпус 3, три штампованных фрикционных клина 4, штампованный нажимной конус У, наружную 5 и внутреннюю 6 пружины и стяжной болт 7 с гайкой 2. Масса аппарата 134 кг. Детали его изготавливают из стали марок: пружины —60С2ХФА (ГОСТ 14959—79); корпус — ЗОГСЛ-Б, или 32Х06Л-У; болт с гайкой — сталь Ст. Зсп5 (ГОСТ 380—71).
Аппарат работает следующим образом. При сжатии усилием 240 кН клинья начинают перемещаться по горловине внутрь корпуса и сжимать пружины. Между горловиной и клиньями возникают силы трения, пропорциональные давлению между трущимися поверхностями. Давление клиньев на корпус увеличивается по мере сжатия пружин и к концу хода аппарата оно достигает наибольшего значения. Чтобы клинья при своем перемещении не смещались в одну сторону и не перекашивались, горловина корпуса аппарата выполнена шестигранной. Окончанием хода аппарата считается положение, при котором нажимной конус полностью входит в корпус аппарата, а упорная плита касается горловины корпуса. После уменьшения сжимающей силы происходит восстановление (отдача) аппарата за счет упругих сил пружин. Для облегчения возвращения клиньев в исходное положение грани горловины корпуса выполнены с наклоном 2°. Основные параметры аппарата определяются при испытании его на прессе по рабочей диаграмме.
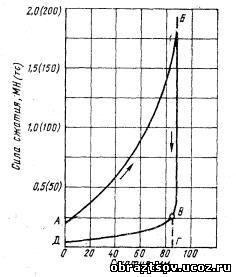
Площадь ОАБГ на диаграмме характеризует энергоемкость аппарата, площадь ДАБВ - необратимо поглощенную энергию, а ОДВГ - потенциальную энергию деформации пружин, которая обеспечивает возвращение деталей в исходное положение. Точка А соответствует начальному сжатию аппарата, а точка Б сжатия.
Сборка аппарата ведется в такой последовательности. В отверстие корпуса вставляют стяжной болт 7, под головку которого устанавливают временную прокладку, исключающую его поворот при навинчивании гайки. Затем ставят две пружины, на которые укладывают три фрикционных клина, а на них — нажимной конус. Собранный аппарат сжимают под прессом, на болт навинчивают гайку, под которую ставят временную подкладку, обеспечивающую свободную постановку поглощающего аппарата на вагон. После первого удара подкладка выпадает, а аппарат занимает нормальное положение в распор между задним и передним упорами.
Пружинно-фрикционный аппарат ЦНИИ-Н6 применяется на пассажирских вагонах.
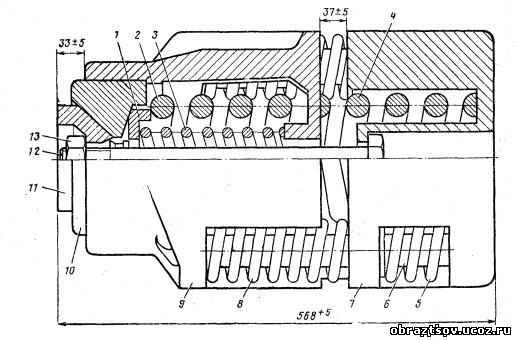
Он состоит из двух частей: пружинной и пружинно-фрикционной. Корпус его также разделен на две части: горловину 9 и основание 7. К пружинно-фрикционной части относятся: шестигранная горловина 9, три фрикционных клина 10, нажимной конус 11, шайба 1, наружная 2 и внутренняя 3 пружины. Конструкция этой части аналогична аппарату Ш-2-В. Пружинная часть состоит из основания 7, центральной пружины 4, четырех угловых пружин 8, надетых на цилиндрические приливы в нишах горловины, четырех малых угловых пружин 5, размещенных в нишах основания и четырех упорных стержней 6. В Стержни проходят внутри больших и малых угловых пружин и разделяют их средней утолщенной частью, находящейся в отверстии основания. Пружины 4 11 2 взаимозаменяемые, 8 и 3 имеют одинаковые размеры и также взаимозаменяемые между собой. Обе части аппарата стянуты болтом 12 с гайкой 13.
Для сборки аппарата в отверстие основания со стороны днища вводят стяжной болт 12, затем в ниши устанавливают малые угловые пружины 5, внутрь пружин вставляют упорные стержни б, а в гнездо основания — центральную пружину 4. На упорные стержни 6 надевают большие угловые пружины 8. После этого ставят горловину 9 так, чтобы ее цилиндрические приливы в нишах по углам вошли внутрь больших угловых пружин 8, а днище легло на центральную пружину 4. Затем в горловину ставят наружную 2 и внутреннюю 3 пружины, на них укладывают нажимную шайбу 1, три фрикционных клина 10, нажимной конус 11, навинчивают гайку на болт и торец его расклепывают.
Работает аппарат в такой последовательности. При воздействии нагрузки сначала сжимаются на 23 мм центральная 4 и четыре большие угловые пружины 8. В этот момент цилиндрические приливы горловины коснутся торцов упорных стержней 6, стержни начнут продвигаться к основанию, а они своими буртами сжимать малые угловые пружины 5. Дальнейшее сжатие аппарата продолжается до тех пор, пока дно горловины 9 не соприкоснется с основанием 7. Прежде чем это произойдет, в работу вступает пружинно-фрикционная часть. Это начинается в момент начального сжатия малых угловых пружин. Вследствие того что конечное сопротивление пружинной части более чем в два раза превышает усилие, приводящее в движение фрикционные детали, обеспечивается плавный переход от работы пружинной к совместной работе обеих частей.
После упора горловины в основание сжатие пружинной части прекращается и работает только пружинно-фрикционная часть.
Сжатие аппарата заканчивается, когда торец нажимного конуса окажется заподлицо с наружной кромкой 1 горловины.
Конечное сопротивление аппарата составляет 1,5 МН, энергоемкость аппарата 18—24 кДж, а коэффициент поглощения энергии — 0,75.

Гидрогазовые поглощающие аппараты разработаны в двух разновидностях: ГА-100М и ГА-500.
Аппарат ГА-100М имеет цилиндрический корпус 1, нажимной поршень - стакан 2, внутри которого размещен плавающий поршень 3, промежуточное дно 4, закрепленное в корпусе, второй плавающий поршень 5, шток 6, который проходит через промежуточное дно и упирается одним концом в поршень 5, а другой конец штока свободно проходит в отверстие поршня 2. В поршне 2 находятся дроссельные каналы 7 и перепускные пазы 8. Аппарат имеет три основные полости А, В, С. Полость А низкого давления заполняется нейтральным газом — азотом при начальном давлении 0,4 МПа, полость В заливается рабочей жидкостью АМГ, полость С высокого давления заправляется нейтральным газом при начальном давлении 9 МПа.
Под действием внешней нагрузки поршень 2 перемещается внутрь корпуса вдоль неподвижного штока 6. При этом рабочая жидкость через каналы 7 и пазы 8 перетекает из полости В в пространство йь воздействуя на плавающий поршень 3, перемещая его влево и обеспечивая сжатие газа в полости А. При дальнейшем движении поршень 2 упирается в выступ штока 6, перекрывает пазы 8, увеличивая гидравлическое сопротивление аппарата. Затем шток 6 начинает перемещаться вправо, давит на плавающий поршень 5, преодолевая давление сжатого газа в полости С. Возвращение частей аппарата в исходное положение происходит за счет упругих сил сжатого газа в полостях А и С. Ход аппарата 70 мм, энергоемкость 100 кДж при силе 2 МН.
Отличие аппарата ГА-500 от ГА-100М состоит в том, что в ГА-500 газовые камеры работают последовательно, поэтому их сопротивление не суммируется, а в ГА-100М газовые камеры работают параллельно и сопротивление их суммируется. Применение газа высокого давления вместо пружин создает большее упругое сопротивление, улучшая работу аппарата при медленном нарастании сил.
Сложность конструкции и трудность обеспечения на длительное время надежных уплотнений, не допускающих вытекание газа и жидкости, является недостатком гидрогазовых аппаратов.
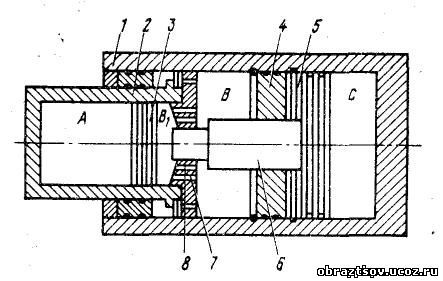
|